Pneumatic Actuated Ball Valve knowledge
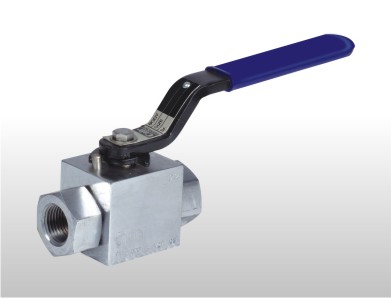
As the power source for pneumatic valve actuators, pneumatic 2 Way ball valves use air (or other gas) and air pressure to operate linear or quarter-turn valves. When air pressure is applied to a piston or bellow diaphragm, linear force is applied to the valve stem. Additionally, a quarter-turn valve can be operated with a quarter-turn vane-type actuator that produces torque. A pneumatic actuated ball valve or pneumatic actuator can be spring-closed or spring-open when air pressure overcomes the spring. You need to know whether the spring is normally open or normally closed based on the function of your application.
In a “double acting” actuator, the air is applied to different inlets, moving the valve in an opening or closing direction. For pneumatic actuators, a central compressed air system can provide clean, dry compressed air. In some types of compressed gas regulators, supply pressure is provided from the process gas stream, while waste gas is vented to air or dumped into lower-pressure process piping. Basic mechanics of Pneumatic 2 Way Ball Valve systems can be found here.
ACTUATION
Mechanically or manually actuated ball valves are pneumatically actuated. Generally, manually actuated mechanisms use screw thread stems, quarter-turn rotary levers, or toggle levers.
In an automat system, valves often operate in inconvenient locations and use a hazardous fluid.
These three types of pneumatically operating ball valves: normally close, normally open, and double-acting. The valve normally closes the spring, so pneumatic pressure moves the valve to the opposite position, and it is in the close position when it is in the normal position. A normally open valve is open when the system is in a normal condition. In double-acting actuators, there are no springs and pneumatic pressure needs to open and close the valve. In addition to direct-mounted actuators, pneumatic actuators can include solenoids. Electrical signals from outside control system sources control its function.
Features :
- Normally, Nomina pipe sizes are between 1/8 inch and 2 inches, with a working pressure of 10,000 psi (690 bar) and a temperature range of -65°F to 450°F (-54°C to 232°C).
- As low as 6 bar air supply pressure with low air consumption. Valve status and other interfaces that meet ISO 5211, NAMUR, and VDI/VDE 3845 standards display on the top indicator.
- Certification is available for explosion-proof products.
NOTES:
The following are some notes on the actuation process:
- When there is an air failure, the valve will remain in the position where the operation disrupts.
- Upon air failure, the valve will return to its original normally open or closed state.
- A failure of air will cause the valve to return to its original normally open state on the left end or right end.
Pneumatic Actuator Operating Conditions
- Source of air
- Air that is dry and clean.
- The pressure of the air supply
- The recommended pressure is 6 bars.
- The maximum pressure is 8 bars.
- The lubrication process
- Under normal operating conditions, factory lubricated for the life of the actuator
- The installation
- Whether install indoors or outdoors, the actuator orient in any direction.
- Two-way ball valve pneumatic actuator temperature range: 5°F to 176°F (-15°C to 80°C) and three-way ball valve pneumatic actuator temperature range: -40°F to 176°F (-40°C to 80°C).
Pneumatic Actuator Operating Principle
Here is how a pneumatic actuator operates when pressure applie to the spring to move the actuator, so the valve can open or close.
Valve Operating Torque
The actuator’s start (break) torque must be greater than the valve’s start torque to begin actuating the valve. The end torque (run torque) the torque require to complete the valve actuation. The torque at the end of the actuator must exceed the torque at the end of the valve.
Factors that Affect Operating Torque
Frequency of Use
As the time interval between cycles increases, the operating torque typically increases as well. Calculating Operating Systems can use for applications where valves do not cycle as frequently as they should.
Cycle Wear
A ball valve, a seat, and a body are in contact. For example, valves gradually wear out as they repeatedly act, resulting increas friction and torque. In addition to actuator speed, valve wear can also influence actuator speed.
Seat or Packing Material
Depending on the material and lubricant, friction between the ball and seat or packing affects operating torque in some ball valve designs.
System Pressure
Higher pressures will result in greater contact forces and friction, resulting in higher operating torques.
System Temperature
The operating torque requirement can increase at lower or higher temperatures depending on the valve design.
System Media
Different fluids have varying viscosities, resulting in different levels of friction and torque effects. Some lightweight oils may reduce operating torque. The operating torque may increase if the fluid is dirty, abrasive, or highly viscous.
Also, read “Common Industrial Valves need to Know“